Knowledge Centre
As of today, the challenge of handling of plastic waste globally persists. One of the solutions to tackle the problem is chemical recycling using pyrolysis technology. But what exactly is pyrolysis, how does it play a key role in recycling plastic waste, and why is it a game-changer?
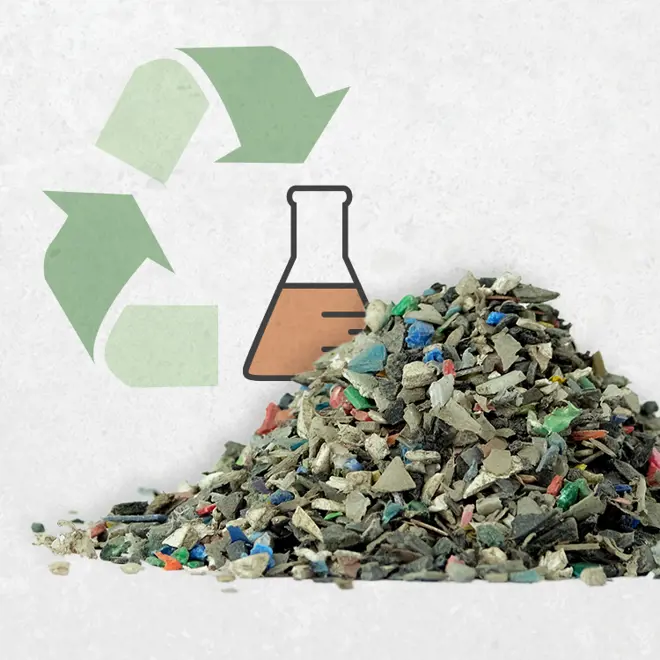
Basics of chemical recycling
Before talking pyrolysis, it is relevant to establish the definition of the umbrella term “chemical recycling”. Chemical recycling is a process that converts complex waste materials, like plastics, textiles, biomass, and other organic substances, into basic building blocks or valuable chemicals through chemical reactions. The process breaks down the materials at a molecular level, restoring them to simpler forms that can be repurposed.
Chemical recycling includes various processing methods, but typically involves breaking down materials into their original form or converting them into gases and oils. By doing this, chemical recycling allows us to recover high-quality materials that can be used to make new products or chemicals, reducing the need for extracting of new raw materials.
This method is particularly effective for handling plastics that are not suitable for mechanical recycling due to contamination or complexity. One of the key methods of chemical recycling is pyrolysis, which breaks down complex materials into simpler substances using high temperatures. But how exactly does that work with plastic waste?
Pyrolysis 101
You may know the word ‘pyrolysis’ from your oven at home. When turning on the pyrolysis setting, the oven cleans itself using very high temperatures – essentially burning the dirt in the oven and turning it into ashes. However, pyrolysis technology is very versatile and is utilised for a lot more than just cleaning ovens. In fact, it plays an essential role in various processes for different industries - one of them being recycling of plastic waste.
Put simply, pyrolysis is a process in which an organic material, such as plastic waste, is decomposed through in exposure to high temperatures, typically between 400°C and 800°C, in an oxygen-free environment. This means that per definition, your oven does not actually use pyrolysis!
By using pyrolysis technology, it is possible to recycle plastic waste from both industry and households with minimum of pre-treatment, producing valuable raw oil products that substitute fossil-based commercial products. A key component of this process is thermal cracking, where the plastic waste is broken down into smaller, more useful molecules through the application of heat.
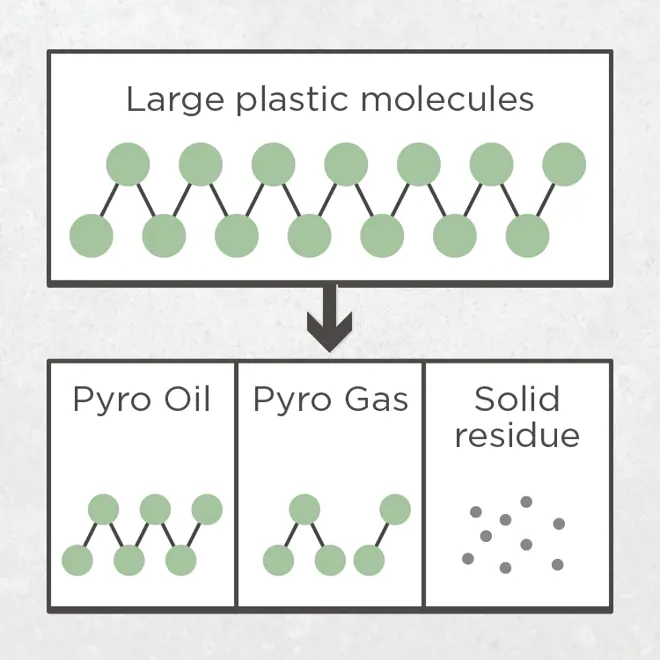
Thermal cracking in pyrolysis
So, what is thermal cracking? Thermal cracking is a process where the large hydrocarbon molecules in the polymer chains (which plastic is made from) are broken down into smaller, simpler molecules by exposing the material to high temperatures. While pyrolysis is classified as ‘chemical recycling’, the main driving force is thermal energy.
In the context of pyrolysis for recycling plastic waste, thermal cracking plays a crucial role. As the plastic waste heats up in the pyrolysis reactor, the thermal energy causes the bonds between the atoms in the long polymer chains to vibrate intensely and eventually break into shorter hydrocarbon chains.
During thermal cracking, catalysts are often used to make the process more efficient. Catalysts are not consumed in the reaction and do not directly break down the plastic. Instead, they assist the reaction, allowing it to occur at lower temperatures or faster rates. Because they are not consumed, only a small amount of catalyst is needed to aid the chemical reaction.
It is impossible to control the exact size of the polymer chains, as they break randomly in this process. Because the breaking is unpredictable, some might be very short, forming gases, while others could be medium or long, forming liquids like oil. The gas can potentially be captured and used as energy source for households or district heating. For the pyrolysis oil, it can be refined as feedstock for producing new plastics or used as fuel.
Thermal cracking permits the pyrolysis to process a wide range of plastic types. This allows for greater versatility in the feedstock of plastic waste – thereby allowing more plastic to be successfully recycled.
Pyrolysis of plastic waste
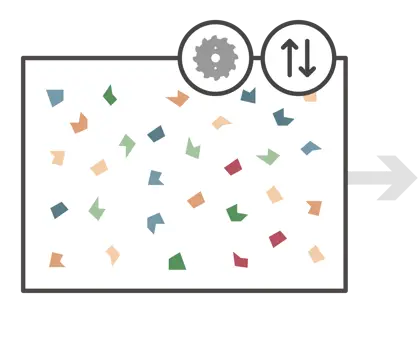
Preparation
1. Plastic waste is collected, shredded into small pieces, and sorted.
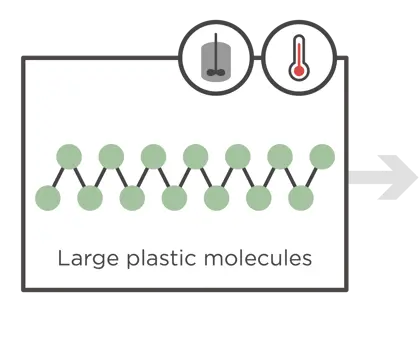
Heating
2. The shredded plastic is fed into a reactor and heated to high temperatures. The high temperature is essential for breaking down the long polymer chains in the plastic.
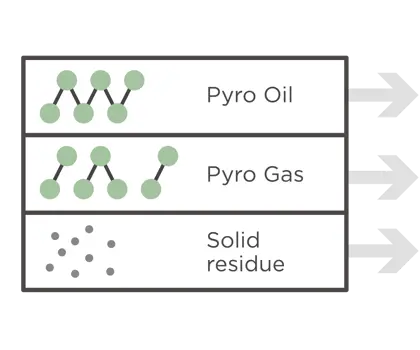
Thermal cracking
3. The heat causes the long chains of hydrocarbon molecules in the plastic to vibrate intensely and break apart. This part is the thermal cracking.
4. The long molecules are broken into shorter molecules, ultimately leading to a mix of gases, oil, and solid residue.
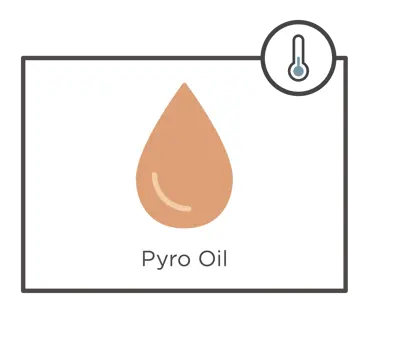
Cooling and condensation
5. Some of the gases from the process are cooled and condensed into liquid form, resulting in pyrolysis oil.
6. The non-condensable gases are collected separately and can be reused as an energy source
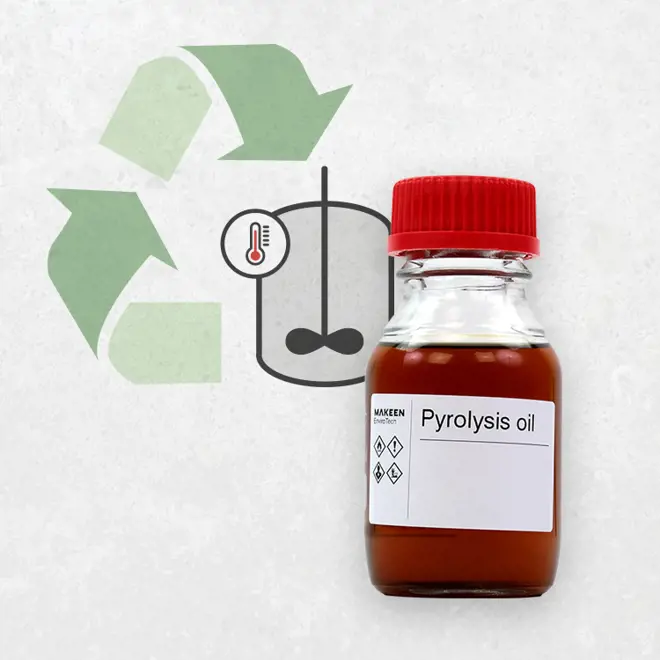
Temperature is key
As mentioned, the nature of polymer product chains cannot be controlled, however, the general outcome can be influenced – and to do so, the right temperature is imperative. Here, it is relevant to talk about “final boiling point”. The final boiling point is the temperature where the last components of a mixture evaporate. In the case of pyrolysis oil, which has a wide boiling range, various components boil off at different temperatures before reaching this final point - this is due to the complex mixture of hydrocarbons in the pyrolysis liquid.
Think of it like cooking: if you heat something to a certain temperature, some parts will evaporate as steam, while the rest stays in the pot. The final boiling point is when the last bits in the pot evaporate. When it comes to pyrolysis of plastic waste, the temperature can be adjusted to find the sweet spot, where the optimal balance of gas and oil is mostly likely to be achieved.
If the temperature is too high, you might produce more gases and very light liquids, which are not as desirable as heavier oils that can be refined into fuel or feedstock for new plastic. On the other hand, if the temperature is too low, processing time becomes too long and the production capacity drops significantly – therefore, temperature is key.
The potential of pyrolysis oil
Pyrolysis oil offers an alternative to traditional fossil fuels and raw materials. The oil can be used in e.g. refineries to produce new plastics, and other valuable products, without investing in new equipment. Because it can be refined in the same way as conventional crude oil, the pyrolysis oil is both a convenient and responsible way to repurpose plastic waste and reduce environmental impact.
Here are some of the ways pyrolysis oil can replace crude oil in existing processes:
1. Making new plastics:
Pyrolysis oil can be processed into chemicals like ethylene and propylene, which are used to make new plastics, effectively recycling waste materials into valuable raw materials.
2. Raw material for chemicals and plastics:
The oil can replace conventional naphtha at chemical plants, which produce essential building blocks for various chemicals and plastics, allowing refineries to use recycled feedstocks.
3. Infrastructure
At large-scale plants, it can be challenging to modify existing infrastructure, with cost being a considerable factor. Therefore, pyrolysis oil offers a great alternative to fossil fuel-based crude oil, as it can be used with the same equipment, reducing the need for additional investment.
4. Fuel alternative
Pyrolysis oil can be mixed with regular crude oil and processed in existing refineries to create products like gasoline, diesel, and kerosene. This offers a great alternative to refineries who are looking towards transitioning into less emission-heavy fuel, supplementing the crude oil with pyrolysis oil.
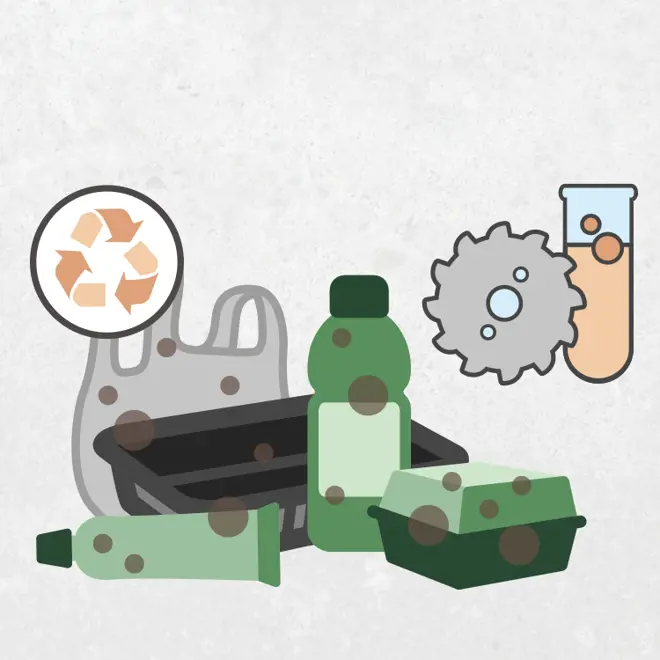
In collaboration with mechanical recycling
Despite chemical recycling being an excellent recycling choice certain types of feedstocks, some are more suited for other methods – here, assistance from mechanical recycling is necessary.
When building a robust and versatile recycling system, both mechanical and chemical recycling methods are essential. Utilising both not only maximises the recycling rates of various types of plastic waste but contributes to resource conservation and working together on the reduction of plastic waste. Mechanical recycling is efficient and energy-efficient for processing plastics that are uncontaminated and uniform in composition, contrary to chemical recycling handling the dirty and complex waste.