Knowledge Centre
Let's talk chain conveyors. Alright, that may not be the best conversation starter in a lot of settings, but in our industry, the chain conveyor is an absolutely essential element. If you are in any way familiar with this staple of many gas filling plants, you most likely know that they don't last forever. Continuous use wears them down until they need to be replaced. The good news is that there are a number of things you can do to maximise your chain conveyor's lifespan, and it all begins with having the proper knowledge.
Wear pattern - not all wear is equal
Here's a fact you may not be aware of: In a properly made chain conveyor system, the different parts are carefully designed to control exactly which of them will wear down first. We call this the wear pattern, and it is not something you can afford to ignore.
To put it simply, a chain conveyor is made up of two components: the chain and the track. Under optimal circumstances, your chain will always be the part that wears down first. The reasons for this are:
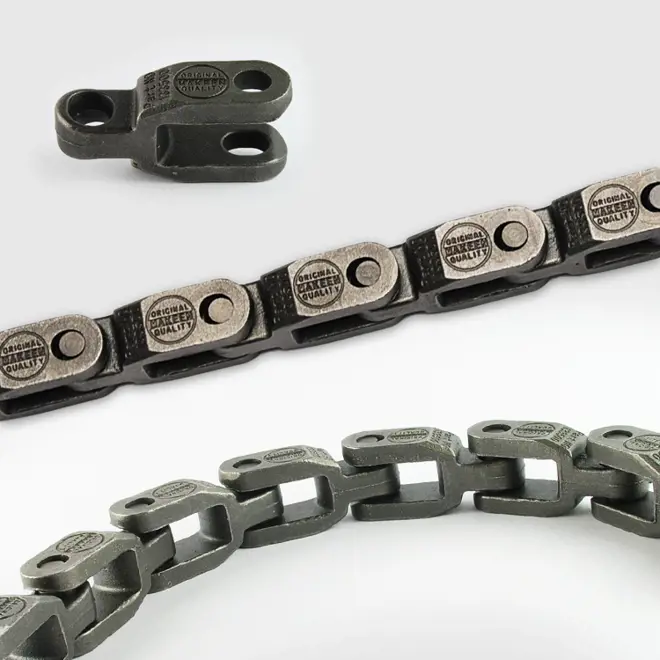
- The chain is easier and much cheaper to replace.
- You can have spare chain sections on hand ahead of time for when some need replacing.
- With the right planning, production only needs to stop for a few hours while your personnel replaces worn sections.
Compare this to changing a section of the track: You have to order a new section from your supplier, wait weeks or even months for it to arrive, and it needs to be installed by a trained technician. During this time, your production output is significantly reduced, if not at a complete standstill. The costs can be staggering.
Achieving the right wear pattern
Correctly balancing your chain conveyor's wear and tear is not something that you can do on the spot in one day – it is a matter of proper design and choice of materials. The good news is that if you bought original equipment from one of MAKEEN Energy's brands, we have done the work for you. An important aspect of our design process is that the steel used in our chain segments is ever so slightly softer than the steel used in our tracks. The difference in softness is big enough, however, to control the wear pattern and ensure that the two materials do not generate sparks when they touch – a crucial safety consideration.
In some places, such as in a 90 degree curve, it is inevitable that the track will experience some wear. To combat this, we cover the track with antistatic polyethylene in the most exposed places. This covering will wear down and have to be replaced from time to time, but this too is much cheaper and faster than suffering direct wear to the track itself.
Did you know?
In equipment cost alone, one meter of track is at least 10 times as expensive as one metre of chain, and it is also much more complicated to replace.
Advanced tip
With proper monitoring and calculations, you can often predict, down to the exact date, when your conveyor chain will need replacing, which allows you to order new parts well in advance. This is not true for the conveyor track – if it wears down, you will not know it before it is too late.
Wet chain vs dry chain
There are two common types of chain conveyor: dry and wet. Determining which of these will work best for you depends on your location and your personal preferences. Both types come with their own advantages and considerations.
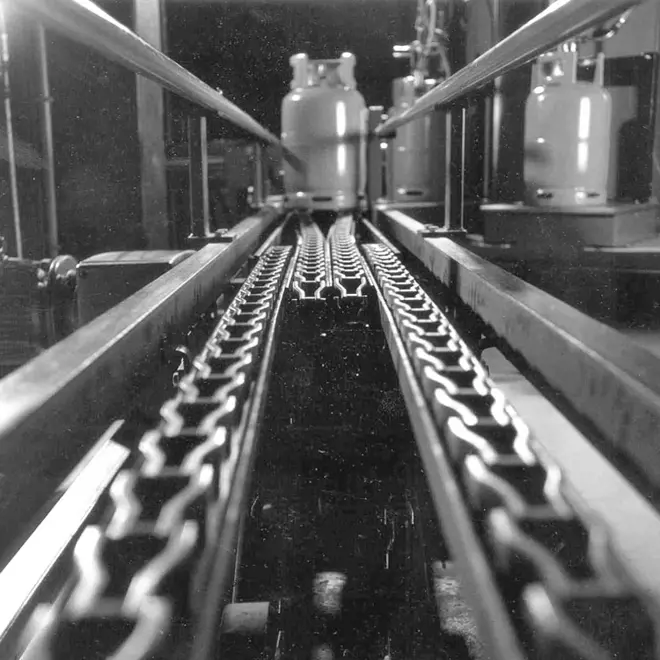
Wet chain
The wet chain is lubricated using black soap or soapy water containing a certain amount of oil or grease. This has two advantages: It keeps the chain moving smoothly, and it eliminates the risk of sparks. The wet chain accommodates both of these functions very well. The drawback to wet chains is that the water evaporates over time, leaving greasy residue that has to be cleaned off regularly. If there is a leak in the track, the slippery soap can spill onto the floor and create serious safety hazards. And lastly, the wet and greasy chain can accumulate dust and grime from dirty gas cylinders. The wet chain demands that you pay careful attention to the maintenance and household of your plant, in order to ensure the safety of your staff as they move about.
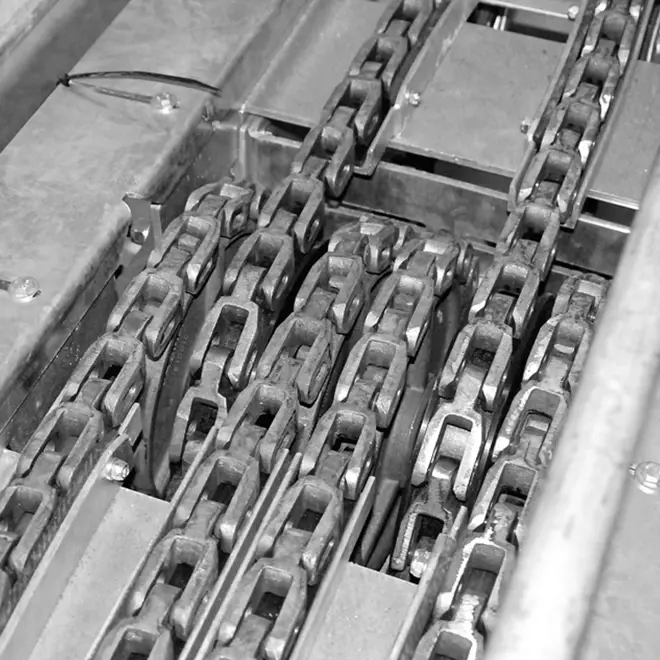
Dry chain
The dry chain, on the other hand, has no soap sloshing around. The chain can be lubricated to reduce wear using an oil spray or Teflon coating, which is easy to control but more expensive than soap. The use of a dry chain involves less maintenance and cleaning, but the absence of soap means that it can wear down a little faster than the wet chain. In areas with limited access to water, such as the Middle East, the dry chain is usually the go-to option. Furthermore, the dry chain does not require additional equipment – such as mixing tanks and pumps – that also needs maintenance.
NOTE: MAKEEN Energy chain conveyors use our own special chain, MCC-30, that we have designed to require less maintenance and be more robust than the market standard.
6 steps to chain conveyor success
#1 Keep it clean
No matter what type of chain you use, regular cleaning is a must. Chains accumulate dirt, dust, and grime that will inhibit their movement or cause wear and damage to your equipment.
#2 Control your wear pattern
All parts wear down eventually. By making sure that it is your chain – not your track – that wears down, you can avoid spending a fortune and precious time on repairs.
#3 Stock up on spare parts
Identify which parts are most likely to need replacing, and order them in advance to save time. Consult with our service experts if you are in doubt.
#4 Trust in quality
The initial investment may be higher, but good quality equipment and parts will always save you money and headaches in the long run.
#5 Use only certified providers
When you buy parts from third-party providers, you risk buying parts that are not designed to fit into the rest of the configuration, resulting in sub-optimal wear patterns.
#6 Learn from the experts
If you're unsure about whether your chain is set up and running optimally, don't hesitate to seek advice. MAKEEN Energy's service team is always eager to help you out.
Let's talk about your chain conveyors
If you’re familiar with the equipment used in many gas filling plants, you know they don’t last forever. Continuous use wears them down. If you need a replacement or have any questions, please get in touch with us.