Knowledge Centre
LPG cylinders are used every day globally, from cooking to powering machinery. They come in different sizes and materials for various purposes, always ensuring the gas stays safely contained. But did you know that regular cleaning is essential to maintain safety and efficiency? By keeping your cylinders clean, you extend their lifespan and keep properties intact. So, remember to give your trusty LPG cylinders a good wash!
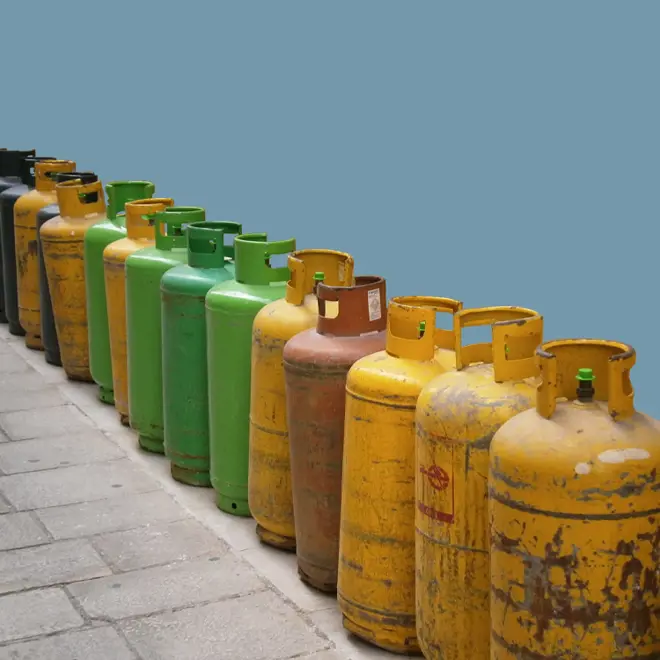
LPG cylinders basic
Quite simply, an LPG cylinder is a portable container for storing and transporting liquefied petroleum gas (LPG). It is a convenient and safe way to deliver LPG to homes, businesses, and industries. Common uses include fuelling cooking appliances, heating systems, and certain types of machinery. And due to the versatility of LPG usage, the cylinders come in various sizes - smaller cylinders are perfect for home kitchens, while larger ones meet commercial and industrial needs.
The material varies, too. LPG cylinders are made from different materials, with composite being the modern choice. Composite cylinders are known for their lightweight nature, making them easier to carry and handle, compared to traditional steel cylinders. Composite cylinders provide excellent durability and safety, thanks to their advanced design and materials, which can handle high pressure and rough treatment, making them a reliable choice for everyday use.
However, LPG cylinders can end up serving many different purposes, so they must be easily adaptable to various kinds of settings. Therefore, they are designed to be strong and secure, ensuring the gas stays safely contained under pressure until needed. No matter its function, all cylinders follow strict regulations for manufacturing, testing, and usage, ensuring reliability and safety. To make sure your LPG cylinders are always adhered to these requirements, they must undergo regular inspections and maintenance.
To give the cylinders the best possible onset, they may be prepped and preconditioned to increase resistance to wear and tear. But despite this preconditioning, LPG cylinders will undeniably be weathered by time. However, you can slow down the process by properly maintaining your cylinders. And when it comes to prolonging their lifespan, there are some low-hanging fruits to pick – one of them is washing.
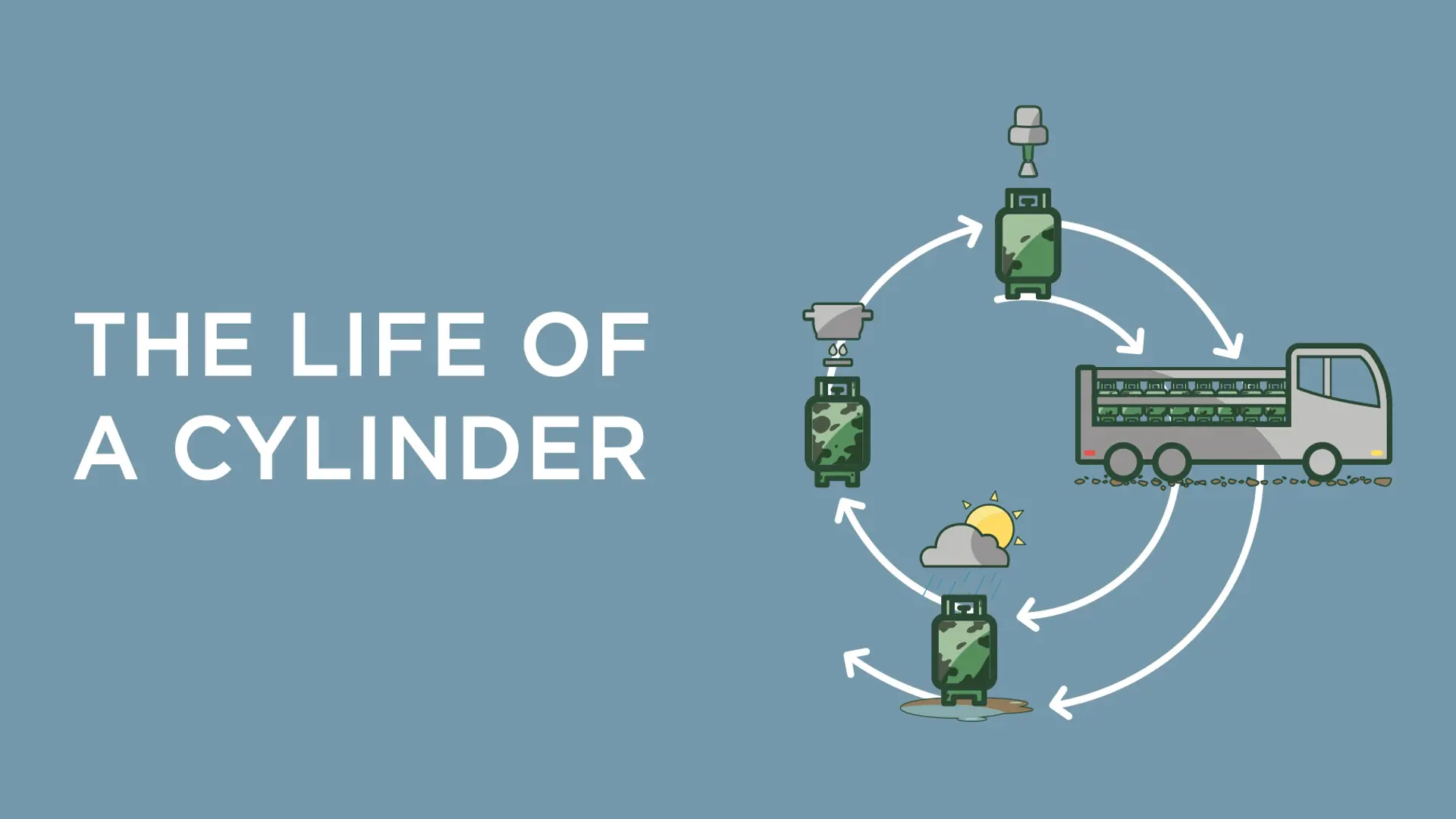
LPG cylinders begin their journey at the manufacturing plant, where they are assembled, painted, and tested. Once manufactured, the cylinders are transported to filling plants. During transit, they can be exposed to road dust, rain, dirt, and other elements, which can cause dirt to accumulate on their surfaces.
The exposure continues when the cylinders reach the filling hall. The filling process involves a lot of handling, where any residue from previous fillings, or the surrounding environment can transfer onto the cylinders. After filling, cylinders are loaded onto trucks for distribution to retailers or directly to consumers. This stage involves yet another move and handling of the cylinders, which can lead to additional dirt and grime. And in some cases, the open nature of transportation can also expose cylinders to weather conditions and road debris.
Once they reach the end user, they are not spared from additional dirt. One is example could be in a household setting, where regular use can lead to stains and marks from cooking areas, such as food splatters or grease. Additionally, the rubber seals and hoses attached to the cylinders might degrade and leave behind particles or residues.
Using LPG cylinders in an industrial setting can also get a bit messy. With all the handling and moving of the cylinders, it is easy for dirt and grime to build up. Industrial areas are often full of dust, chemicals, and debris, all of which can find their way onto the cylinders. Accidental spills during refilling or while connecting and disconnecting the cylinders can leave oily residues or chemical stains. Plus, if the cylinders are stored outside, they can get dirty from exposure to the weather. And with the high usage rate in these environments, there is bound to be wear and tear.
It is safe to say that throughout this journey, every stage involves some level of unavoidable steps that contributes to the dirtiness of LPG cylinders – but what are the consequences of grimy cylinders?

Safeguarding public health
Sometimes, looks do matter. Customers are more likely to trust clean cylinders that reflect safety and high quality, especially if the cylinders are intended for cooking in private homes or at restaurants. Imagine you are going out for a nice meal, and you peek into the restaurant’s kitchen. Undoubtedly, the look of a very dirty cylinder used for cooking can raise concern and reduce appetite.
However, it is not only the look of a grubby cylinder that can be displeasing, but it can pose a serious health risk. All the gunk and grime that have accumulated on the cylinder is a breeding ground for bacteria that might end up in your dinner and you risk getting seriously ill. This also applies to dirty cylinders in your kitchen at home, so these must not be forgotten!
With the high standards of safety within the LPG industry, hygiene and public health is, naturally, also a big concern. Meeting hygiene and safety standards isn’t just about following the law; it’s a smart way to protect public health, and the importance must not
be understated.
Did you know?
There are around 2 billion LPG cylinders in circulation worldwide.
Over 3 billion people in the world rely on LPG cylinders for cooking, heating, and other energy needs.
LPG is a clean-burning, efficient, and versatile energy source with more than 1,000 potential applications.
Compared to burning wood, LPG only produces 1/150 as much carbon monoxide, resulting in a much cleaner indoor environment.
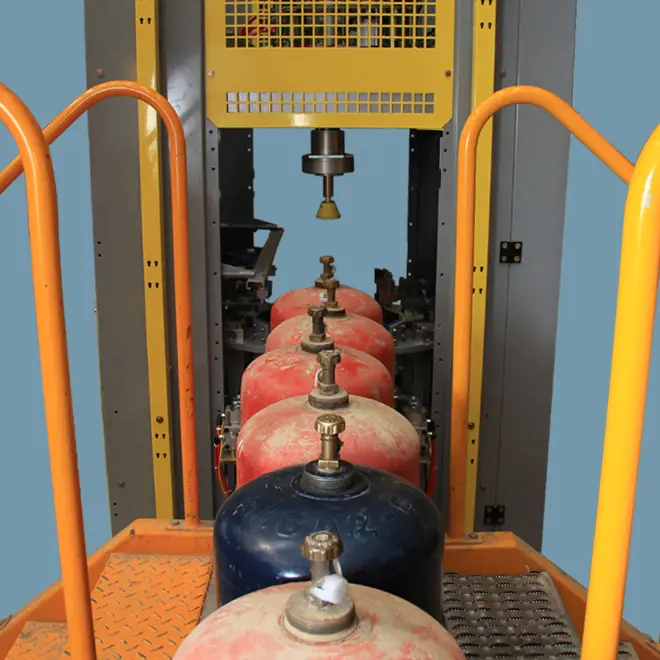
Rules and regulations
A way to ensure the safety of public health when it comes to LPG cylinders, is to prioritise keeping them clean and well-kept. This is a fact also recognised by authorities worldwide, for example the EU, United States, and India, that have implemented several regulations for maintenance and washing of LPG cylinders.
In Europe, the Transportable Pressure Equipment Directive (TPED) 2010/35/EU mandates that pressure equipment, which includes LPG cylinders, undergo regular washing as part of their requalification process. The washing removes dirt, rust, and any residual LPG, which is vital for exposing defects and preventing corrosion.
In the United States, the Department of Transportation (DOT) regulations under 49 CFR Part 180, Subpart C also require thorough washing of LPG cylinders during periodic inspections. This cleaning is essential to remove contaminants that could hide defects or compromise safety. The DOT guidelines ensure that washing is performed using non-corrosive agents, and all steps are documented to maintain safety compliance.
India’s Petroleum and Explosives Safety Organisation (PESO) has similar guidelines that emphasise contaminants must be removed before inspections - this includes rust, corrosion, and other contaminants that could affect the inspection or testing results. Additionally, a visual inspection is also required to examine external and internal corrosion, dents, gouges, and other damage, and to do so, the cylinders must be clean – the solution? A thorough washing.
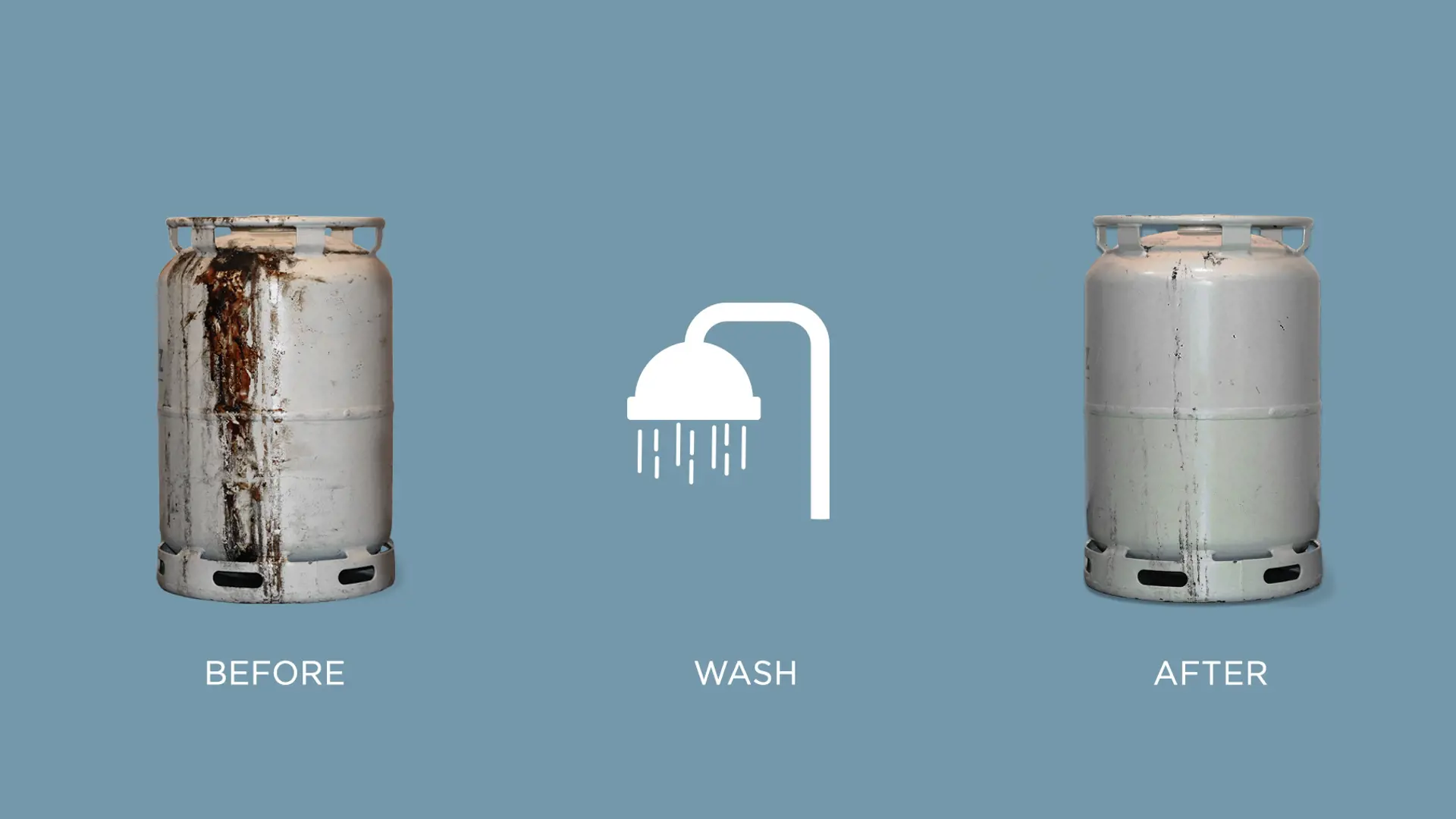
A cost-efficient investment
As mentioned, LPG cylinders are exposed to various environmental conditions, which puts them at risk of rust and corrosion. By regularly washing the cylinders, you remove contaminants that contribute to this corrosion. This effort not only improves the cylinders’ appearance and positively affects your brand image, but prolongs their life span, reducing the need for costly repainting or replacement, saving you money in the long run.
As an added bonus, when choosing an automatic washing system that is designed to recycle and reuse wastewater, you significantly reduce water consumption, not only conserving a valuable resource, but lowers the energy required to heat fresh water.
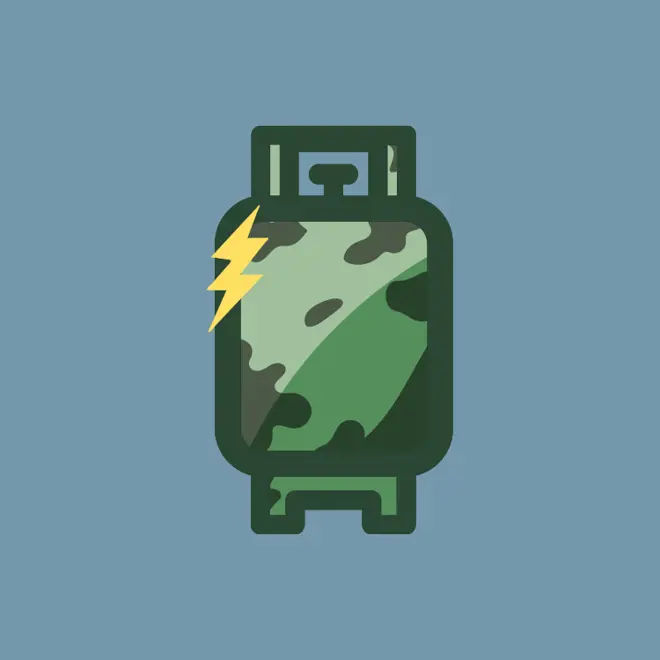
No to static electricity
When an LPG cylinder is filled or in contact with or rubbed against another material, static electricity can accumulate at the point of contact. Static electricity can also be generated by the friction of LPG flowing through the cylinder valve or inside the cylinder. For a steel cylinder this is not a problem, because the cylinder itself is conductive and all static electricity build-up will be discharged through the filling equipment. A composite cylinder, on the other hand, is not made of conductive material and any build-up of static electricity will accumulate in the composite cylinder, mainly in the casing plastic material. If there is a sufficient build-up of static charge, a spark can occur when the composite cylinder is separated from the metal.
This spark is not due to the composite material itself holding a charge but rather the static charge generated at the interface between the composite and metal – like the steel on a conveyor chain. This buildup can pose a safety risk if not properly managed. Luckily, there is a quite simple and easily available tool to solve this: water.
Firstly, water provides a conductive layer on the surface of materials. When a composite cylinder is washed, a thin film of water remains on its surface. This film acts as a conductive barrier, allowing any static charge that might build up to dispel safely.
Secondly, water reduces friction between surfaces. When the cylinder’s surface is wet from recent washing, the water acts as a lubricant, reducing friction. With less friction, there’s a lower risk for static electricity to build up, further decreasing the likelihood of static discharge or sparks.
It is generally recommended by composite cylinder manufacturers to wash the cylinder for safety, as well as for aesthetic considerations. Not only does washing your LPG cylinders reduce the risk of rust and corrosion, prolong the lifespan of the cylinders, positively contribute to brand image, protect public health, help you adhere to regulations and inspection requirements, it can even reduce one of the biggest safety risks within handling of LPG: static electricity.
So, what are you waiting for?
Get to washing your LPG cylinders, rather today than tomorrow!
Download the e-book
Download the e-book and equip yourself with all the knowledge you need to keep your cylinders in pristine condition.
Click below to get your free copy and put these insights to work!