News
It's necessary to look "inside the box" to find opportunities for improvement.
In recent years, we've embraced Continuous Improvement using the Kaizen philosophy, focusing on enhancing processes and developing our workforce. Our commitment to excellence paid off in 2023, when two of our facility management teams in Portugal were recognised for their exceptional dedication and hard work, highlighting our journey towards operational excellence.
Driving efficiency and quality
At MAKEEN Energy, we are committed to a Continuous Improvement approach, emphasising process refinement and development of our people. Our improvement philosophy is based on Kaizen, which means “improvement” or “change better” in Japanese, a practice focusing on long-term and repeated optimisation of internal processes and guiding employees in efficient ways of working. Central to this approach are efficiency, quality, safety, and service. Such improvements directly impact customer experience by empowering teams to tackle inefficiencies, and the organisation becomes more agile with sustainable, meaningful enhancements.
Central to this approach are efficiency, quality, safety, and service. Such improvements directly impact customer experience by empowering teams to tackle inefficiencies, and the organisation becomes more agile with sustainable, meaningful enhancements.
In a world of digitalisation, we have implemented new Continuous Improvement tools to our MAKEEN system. By linking our internal system with PowerBI, we can now access data globally for each division. This system allows us to keep track of improvement opportunities and align colleagues worldwide by easily accessing information and inspiration, making each other good.
Succesful implementation in Potugal
At the end of 2023, our facility management teams at Pergás and Repsol Banática in Portugal achieved a great milestone: the Kaizen Maintenance Certification granted by the Kaizen Institute. The certifications are a recognition of the successful implementation within the respective maintenance departments, securing sustainability and growth their daily work. Daily, the technicians at the plants put all info into the planning tool, Power App, ensuring tasks and resources are aligned so meet daily goals. Additionally, a dashboard has been created for each plant, where progress can be measured to create action plans.
The implementation of the Kaizen philosophy at the two facility management contract plants have resulted in key learnings, which we are using to set the standard in securing Continuous Improvement throughout our operations.
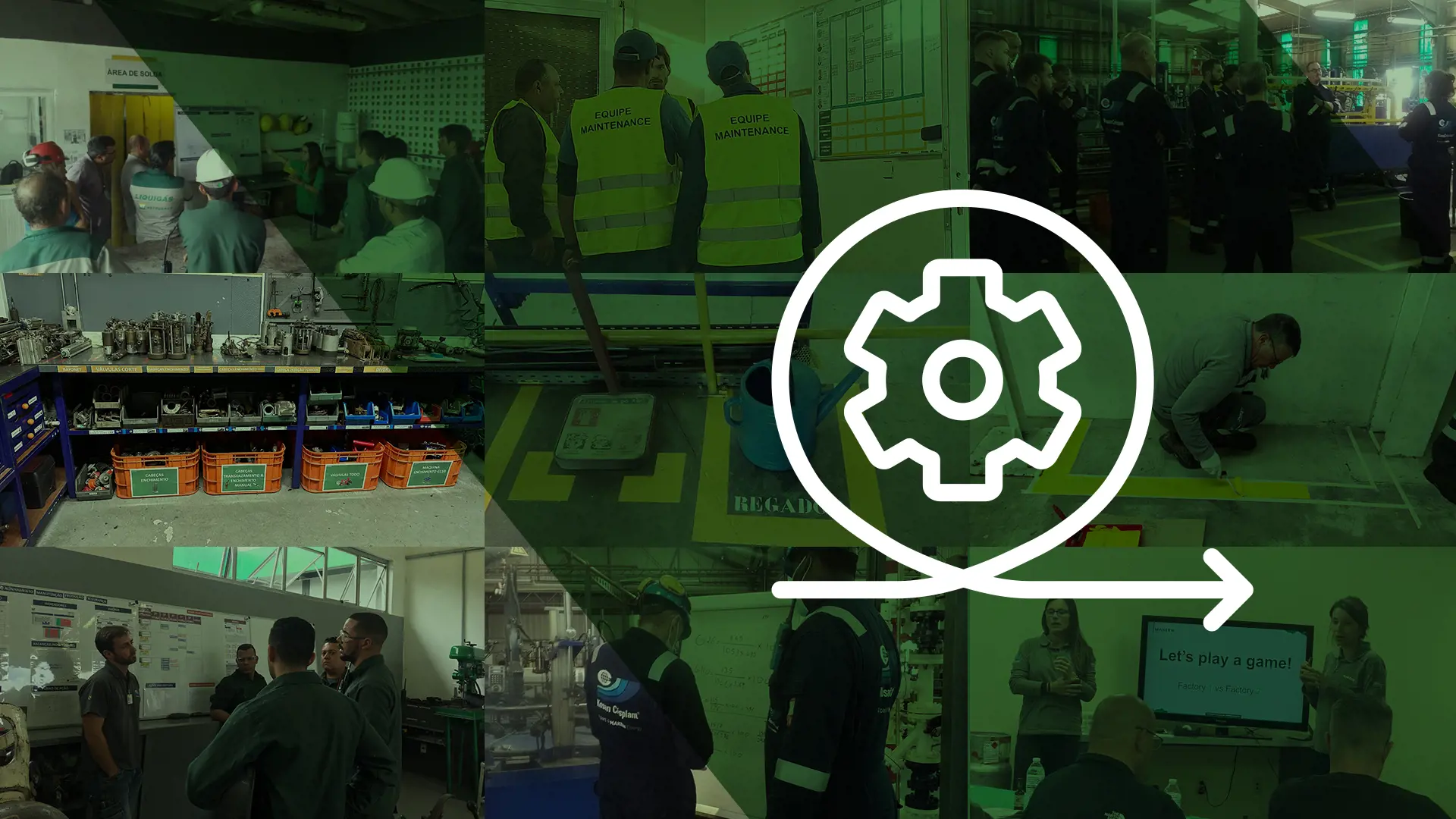