Knowledge Centre
Static electricity is a constant risk wherever highly flammable gas such as LPG is used. It is a threat that can’t be seen easily – but it is always present. Our Maintenance & Asset Manager Carlos travels around the world to educate colleagues and customers alike about the measures you can take to mitigate the risk of static electricity, and he has agreed to share some of his knowledge with us here.
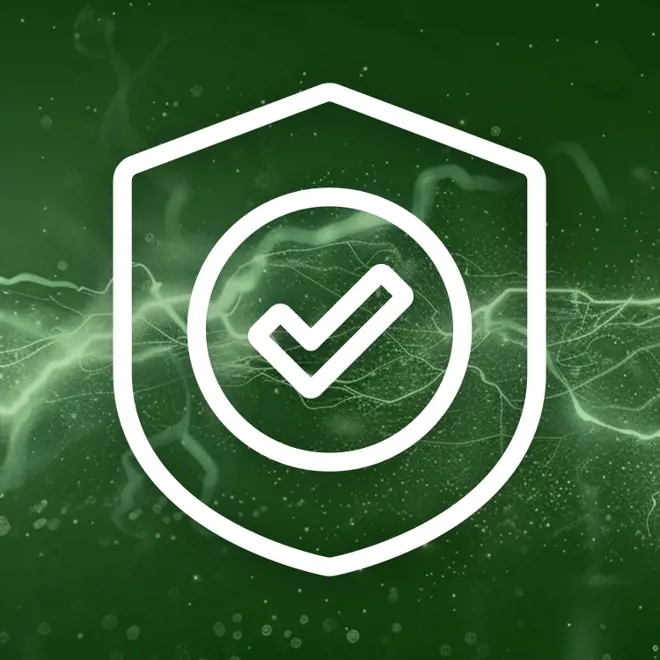
Fire safety in the LPG industry has gotten better and better over the years, and yet we still encounter some persistent myths and gaps in knowledge from time to time. This is particularly true when it comes to static electricity.
If you ask someone to name the most dangerous safety hazards on LPG filling plants, many start talking about smoking a cigarette on the job, a loose wire in machinery, or using a cell phone that is not ex-safe. The thing about these risk factors is that they stick out like a sore thumb, so you can quickly spot them and make adjustments.
Static electricity is different. If you don’t know enough about it, it hides and builds up until one day you get a nasty surprise that can have serious consequences. That is why we put a lot of effort into educating both our own people and our customers’ staff about how to minimise
this risk.
Humidity matters
Carlos has worked with LPG for over 15 years. Most of those were in Brazil, and every year, he has seen reports of fire incidents in plants around the country. There is often a pattern to them; they are significantly more common in dry regions.
Humidity, or the lack thereof, plays a critical role in the accumulation of static electricity. You see, static electricity is only dangerous when it is allowed to build up enough energy. Humid air is more conductive, so the static energy can be easily released. In dry areas, the absence of moisture in the air means that static electricity has no easy path to dissipate. Instead, it accumulates until it finds a release, which potentially creates a spark that is capable of igniting LPG vapours.
Does that mean you are safe if you are in a humid environment? Not entirely. Your risk is lower, but you still need to be aware of it and protect yourself and the people around you.
How do we minimise the risk
Removing plastic:
Plastic is notorious for accumulating static energy, yet it still finds its way to more and more places in LPG filling plants. At MAKEEN Energy, we
prioritise anti-static materials, and that includes special anti-static plastic that lives up to safety certifications.
Anti-static working clothes:
Effective static dissipation is critical, and this also extends to the safety gear we wear on an LPG site. Footwear is especially important, yet often forgotten. Shoes provide the grounding path for static charges accumulated in the body, making their anti-static properties crucial.
Automation of equipment:
A human being is an efficient static electricity accumulator. By removing a
human operator from a process, and minimising human contact with LPG sources, you improve the safety on your site. And that’s in addition to the increased efficiency of automated equipment.
Earthing and electrical continuity:
Ensuring that all machinery and moving parts are properly earthed is fundamental. The electrical continuity of components, particularly those in constant motion, must be maintained to provide a secure path for static charges to dissipate safely to the ground.
Proactive measures:
Don’t fall into the trap of thinking that LPG leaks are somehow normal or unavoidable – that is a dangerous mindset! Any leak that happens could have been prevented with a proactive approach and careful attention to the maintenance of your equipment.
Protecting yourself and your people against fires caused by static electricity requires you to pay attention to several factors, touching on both material selection, equipment design, and a culture of safety and vigilance. Embrace these principles, and you can significantly mitigate the risk of fires, ensuring a safer operational environment for everyone involved.