Knowledge Centre
India accounts for most of our Facility Management contracts for LPG bottling plants. And when managing operations at the plants, safety is always at the core. To uphold this commitment, our Safety Officers are vital. Because of India's key role, the MAKEEN Energy India team excel in extensive training of our Safety Officers, keeping them up-to-date with the latest safety technologies and industry practices. But what does it take to be a Safety Officer at MAKEEN Energy India?
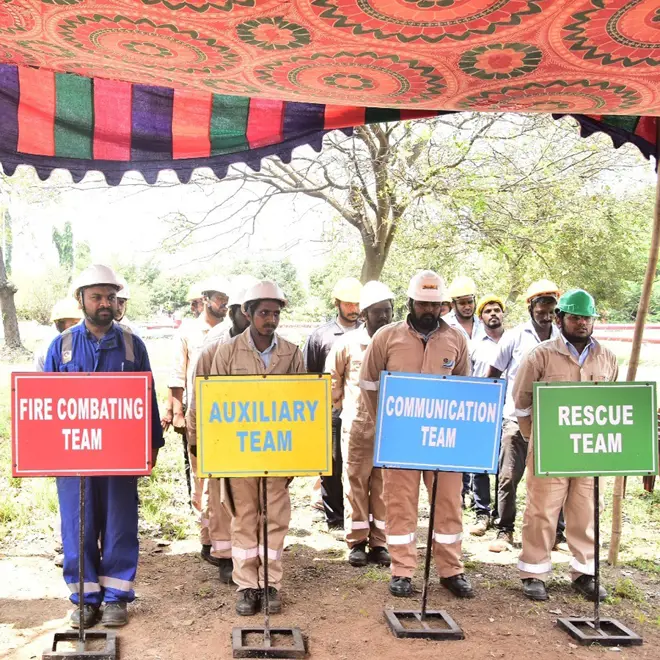
Becoming a Safety Officer
A Safety Officer is main responsible for plant safety, which includes operational safety, orienting maintenance practices according to safety norms, legal compliance with safety regulations, and the upkeep of the firefighting system. With the role comes great responsibility, which is why the importance of choosing the right person for the job is essential. And when doing so, there are several factors to consider:
Educational requirements
A Safety Officer must be a person with a good technical knowledge, preferably with a Bachelor of Engineering degree in Fire and Safety, a Bachelor of Engineering degree in any programme with a diploma in Fire and Safety, or a Master of Engineering degree in Safety.
Technical knowledge
A Safety Officer must have in-depth knowledge of various hazards identification techniques like HAZOP, QRA, HIRA, JSA, etc. He or she must be aware of emergency response and disaster management plans, accident investigation techniques, root cause analysis, and accident reporting systems.
Attention to detail
Possessing a high level of physical vigilance, constantly monitoring the work environment for any potential safety hazards is crucial for a Safety Officer. This entails regular site inspections and the ability to detect changes or non-compliances that others may not notice.
Safety regulations
The Safety Officer must be well aware of statutory rules and regulations like OISD, PNGRB, Petroleum Rules, SMPV Rules, Gas Cylinder Rules, Factories Acts, Air Act, Water Act, Central and State Pollution Control Board norms, etc.
Communications and training
A Safety Officer must be able to convey complex safety information in a way that is easily understandable all employees, regardless of their level of expertise. He or she must be able to engage employees from diverse backgrounds and adapt their training methods to different learning styles to ensure that everyone understands and can apply safety protocols.
Adaptability and problem solving
In the role as Safety Officer one may often face unexpected situations that require quick thinking and flexibility. The ability to adapt to new hazards, changes in the work environment, or evolving industry practices is essential for maintaining an effective safety program. To address these changes, Safety Officers must be able to adjust strategies and plans without compromising employee safety.
Compliance monitoring
One of the Safety Officers' primary responsibilities is to monitor compliance with safety protocols and enforce these rules when necessary. To ensure the meeting of safety standards, Safety Officers must conduct regular inspections, audits, and reviews.
Empowering our Safety Officers
Continuous training in industrial safety is critical for ensuring the well-being of employees and safety of the plant operations. It equips employees with essential knowledge and skills to identify hazards, follow safe practices, and respond effectively during emergencies. By educating employees about potential risks specific to their tasks and environments, safety training significantly reduces the likelihood of accidents and injuries. This not only safeguards individual employees from harm but also fosters a culture of responsibility and vigilance throughout the organisation.
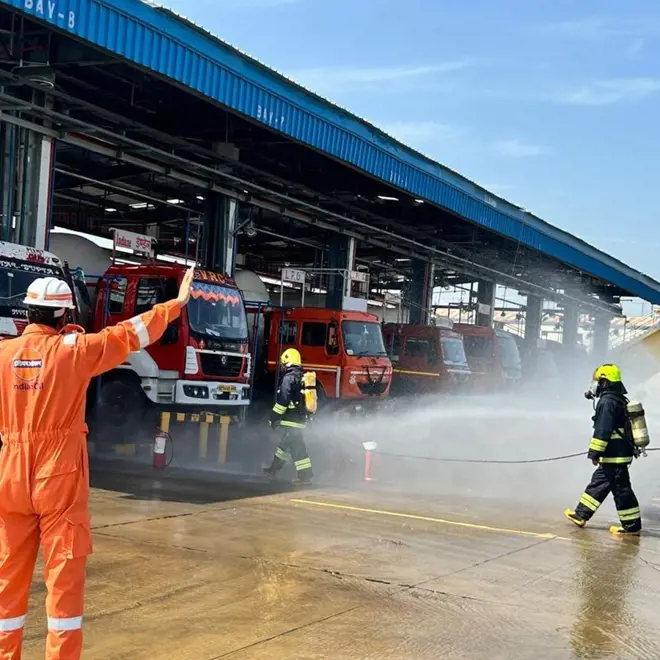
MAKEEN Energy India organise in-plant trainings under OISD guidelines, PESO, and other statutory regulations, which cover all aspects of LPG plant operation, safety, and maintenance.
These trainings are inclusive, involving personnel from all levels—from officers to supervisors, on-roll and contract workers, security staff, drivers, and more. This inclusive approach ensures alignment with safety protocols, ensuring safe operations are conducted only by properly trained personnel. This collective effort fosters a safe work environment that prioritises professionalism and trust among colleagues.
By organising safety webinars and training sessions with experienced trainers, we provide our employees with the opportunity to learn and develop modern skills and stay updated with technological advances, ensuring we maintain the highest QHSE standards.
Keeping up with safety
In a typical safety training session, all levels of workers may attend. The trainers are safety personnel with good experience in plant safety and security inside and out. The training starts with an introduction to help the trainees feel at ease. By conducting a pre-training quiz to assess trainees' knowledge levels, the trainer shapes the discussion or presentation accordingly.
Afterwards, the trainer will then begin by explaining the basics of safety, leading to a thoroughly discussion of each aspect. As our Safety Officers in India are responsible for the safety at LPG bottling plants, the topics are customised for this particular setting - and these include:
- Accident prevention
- Characteristics of LPG
- Safety regulations
- Fire fighting
- Emergency rescue & handling
- Electrical safety
- First aid training
- ... and much more
A field visit is also extremely helpful for trainees to co-relate the theoretical aspects of training delivered with actual installations on-field.
As a final step, a post-training quiz is organised to evaluate the understanding of trainees. The trainer then thoroughly reviews the feedback forms filled out by trainees to identify areas for improvement in training sessions - all to make each other good.