Case: Repsol, Peru (2014)
Customer
Repsol, Peru
The customer's challenge
A growing demand for LPG in and around Lima, Peru
Our solution
An additional filling line with various fully automatic processes
The outcome
- Plant capacity increased by more than 30%
- A higher level of automation
- Reduced manual handling
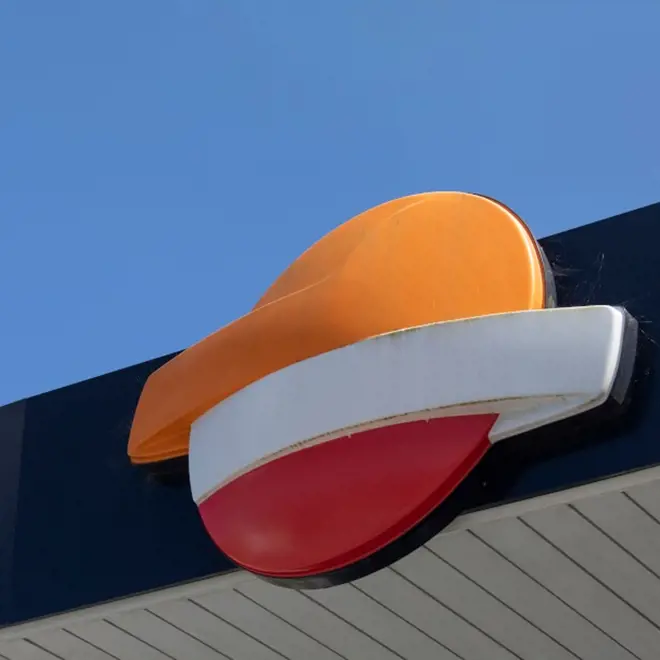
Scope of supply
- Layout
- Installation management and on-site supervision
- Fully automatic carrousel system with 36 UFM filling machines and a capacity of 1600 cylinders/hour
- Chain conveyor system
- Telescopic conveyors for loading/unloading of non-palletized cylinders
- UFM filling machines, equipped with Repsol's own filling heads
- Fully automatic equipment for cylinder orientation, check weighing, leak detection, valve testing, pad-printing, application and sealing of shrinkable caps, and cylinder washing and painting
When Repsol in Peru decided to install a third LPG filling line at their Ventanilla plant, it required extensive cross-border collaboration with Kosan Crisplant (today known as MAKEEN Energy) as coordinator.
Faced with a growing demand for LPG cylinders, Repsol decided to upgrade their Ventanilla plant with a third filling line and put Kosan Crisplant in charge of the project. With several sub suppliers and a local contractor for civil works involved, the project required a large amount of coordination in terms of logistics, communication and getting the different equipment to work perfectly together.
Increased capacity and reduced manual handling
The new fully automatic 36-scales carrousel filling system has a total capacity of 1600 cylinders per hour. In order to reduce the manual handling of cylinders to a minimum, the project also comprised a chain conveyor system and three telescopic conveyors for easy loading and unloading of non-palletized cylinders.
Automation ensures quality
The new filling line also boasts fully automatic equipment for various processes, including cylinder orientation for easy tare value reading, check weighing, leak detection, valve testing, pad-printing, application and sealing of shrinkable caps, and cylinder washing and painting. The automation of these processes has reduced manpower requirements and ensures that Repsol is able to deliver products of a consistently high quality to their customers.
Customer co-creation
The filling plant is designed to process 10 kg cylinders with two types of centre valves. As Repsol Madrid had previously developed a filling head especially for these two types of centre valves, they wanted the Kosan Crisplant UFM filling machines to be equipped with their own filling heads. The task of integrating Kosan Crisplant's filling machines and Repsol's filling head was carried out in close cooperation with Repsol's technical department in Madrid.