CASE: Petronas Malaysia (2014)
Customer
Petronas Dagangan Berhad, Malaysia
The customer's challenge
To fill 75,000 14 kg cylinders per day.
Our solution
To expand the filling hall to make room for a complete FLEXSPEED system
The outcome
Total filling plant capacity more than doubled.
Scope of supply
- Two and three storey palletizers
- Fully automatic vision system for label reading and sorting
- Divert module with four exit lines
- FLEXSPEED carrousel with 72 filling posts (capacity: 4000+ cylinders/hour)
- FLEXSPEED process modules for leak detection and application of hard caps
- Production Tracker monitor in filling hall
- Electricity, civil works, project management, etc.
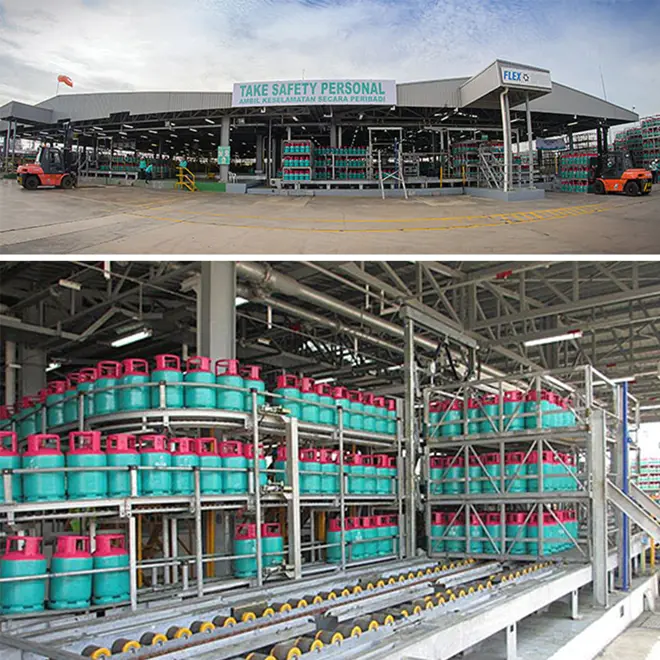
The need to fill 75,000 14 kg cylinders per day at their Melaka plant made Malaysian oil giant Petronas go high-speed with FLEXSPEED. In only 16 months and with a minimum of production downtime, the Melaka plant was expanded and a complete FLEXSPEED system installed. Kosan Crisplant's Malaysian subsidiary carried out the entire project, including civil works, and received two awards for best HSE performance by a main contractor along the way. (Today Kosan Crisplant is known as MAKEEN Energy)
The new plant was handed over to Petronas four days ahead of schedule, and six months after its inauguration it had already filled more than 10 million cylinders.
Improved cylinder logistics
The first part of the project involved the removal of the two existing palletizers and the installation of two new high-capacity palletizers (one two-storey and one three-storey). They ensure that enough cylinders enter and exit the FLEXSPEED system to fill 4000 cylinders per hour.
At the same time a huge part of the existing chain conveyors were moved and new were added; this entire process causing only a week's production stop.
Fast and easy maintenance
The FLEXSPEED system at the Melaka plant includes newly designed filling heads with a modular design for easy maintenance. The design of the entire system has been optimized as well, making it easier and less time-consuming to exchange wearing parts.
The FLEXSPEED system's fully automatic intelligent flow control means that every part of the cylinder transport system is controlled by the CUC, KC's easy-to-use and energy efficient HMI controller. This ensures that the speed of the chain conveyors and the carrousel are automatically adjusted according to each other. The smooth flow reduces both the noise level and the amount of surface damages incurred by cylinders during the filling and checking processes.
Keeping track of production
The Production Tracker, another new feature developed specifically for this project, is a large monitor located in the middle of the filling hall. The monitor converts filling hall production data into easily decodable graphics and ensures that the filling hall operators know at all times whether they are able to meet the shift's production target.
The Production Tracker is an add-on to KC's basic production data management system.